The Benefits of VFDs: Why Choose a Variable Frequency Drive Control Panel?
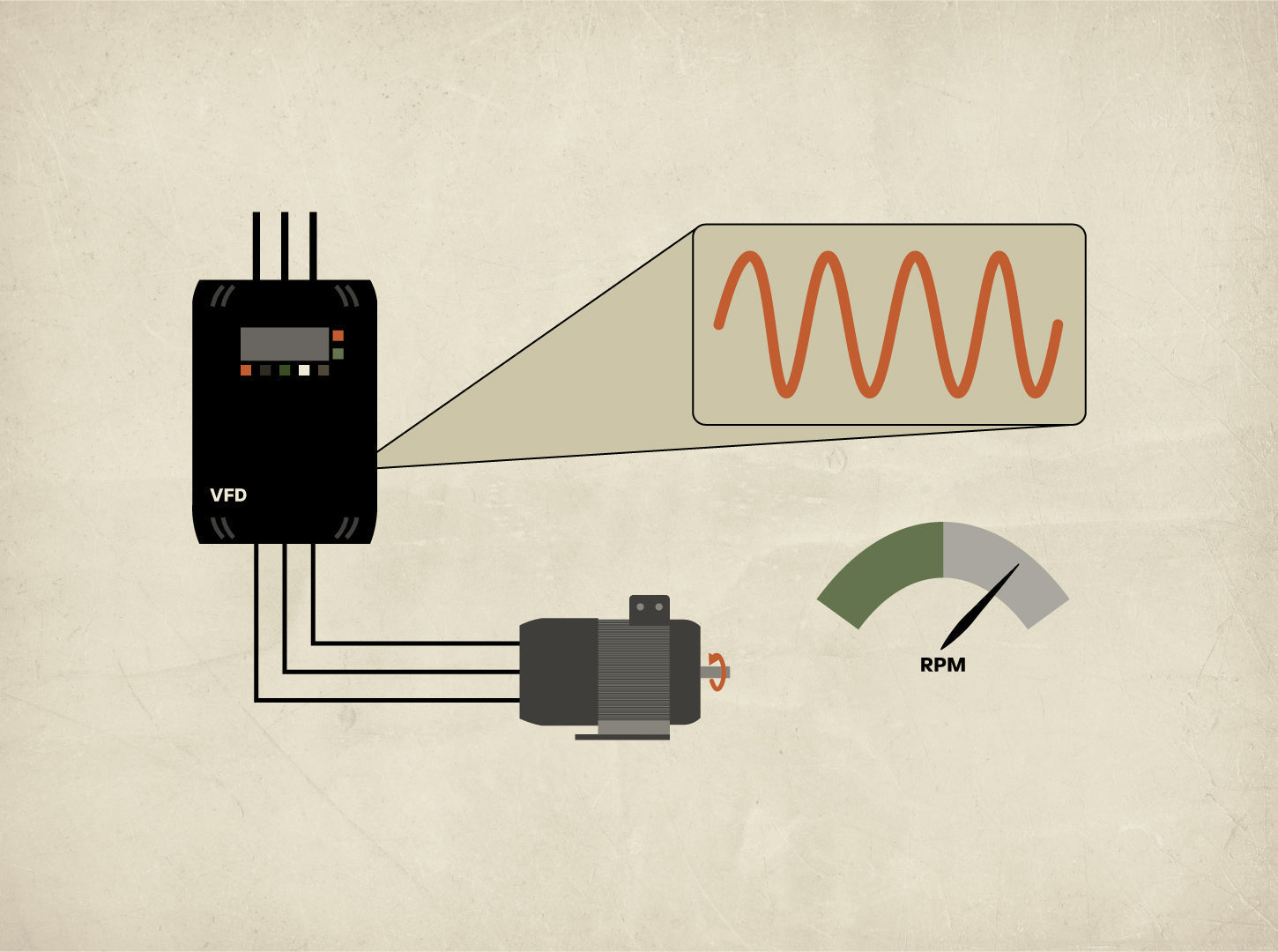
By Anna Niu and Krista Goodman
Last updated November 14, 2024
The Benefits of VFDs: Why Choose a Variable Frequency Drive Control Panel?
Variable frequency drives (VFD) can offer many benefits to pump stations by helping to protect and extend the life of the pump(s) and other components in the pump station.
A pump will normally run at full speed based on the frequency of the supply voltage, which remains at a constant. When a VFD serves as the power supply for the pump motor, it can adjust the frequency of the supply voltage, enabling the pump to operate at various speeds and transition smoothly from one speed to another as needed.
Therefore, VFDs are very efficient in applications where the flow, density, and/or viscosity of the media may vary quite often because the pump speed can be controlled to match the variable demand of the media being pumped.
While VFDs tend to come with a higher upfront cost for your pump control panel, the many advantages when it comes to operational efficiency as well as long-term energy and cost savings are worth consideration.
Variable frequency drives may offer many benefits for your pump(s) and other systems, including:
-
Energy savings: VFDs can reduce electricity costs by as much as 30% by optimizing the motor speed of the pump(s) used in applications such as pressure boosting water supply systems that operate 24/7. Additionally, VFDs are more energy-efficient compared to motors that operate at a constant speed, as they allow for variable motor speeds, leading to significant energy savings.
-
Improved pump control: VFDs can be configured to control each pump’s speed and behavior, which can help protect the pump from damage.
-
Control over flow rate: VFDs will adjust the speed of the pump(s) to control the flow rate of the media being pumped, which can result in substantial cost savings on electricity use. If the pump(s) can run efficiently by pumping at a slower speed, less electricity will be consumed over time to run the pump station.
-
Reduced maintenance: VFDs may reduce the wear and tear on motors and other components in your pump station, which can both extend the life of your pump(s) and reduce the need and frequency for repairs and maintenance. Additionally, VFDs start motors at zero voltage and frequency, reducing mechanical shock and extending motor life.
-
Motor overload protection: VFDs monitor the motor current of your pump(s) and will prevent overloading conditions. They can also be configured to prevent pumps from slowing down below a safe speed.
-
Eliminating water hammer: VFDs allow the pump motor to smoothly transition between stopping and starting, which effectively eliminates water hammer. Water hammer occurs when the media (fluid) in a pipe is forced to stop or change direction suddenly, which causes a pressure surge or shockwave to travel through the pipe system. The pressure increase in the system can seriously damage equipment or rupture pipes within the system.
-
Reduced amount of equipment (in some applications): VFDs can eliminate the need for some of the components that have otherwise been required in traditional system designs. For example, they can eliminate or reduce the number of control valves needed in the system that might otherwise require additional installation and maintenance.
Energy Consumption and Cost Savings
One of the standout variable frequency drive advantages is their ability to significantly reduce energy consumption. By optimizing motor speed and torque, VFDs ensure that your pump station operates only as hard as it needs to, rather than running at full power constantly. This optimization leads to substantial energy efficiency, as the power required to start and run motors is minimized, resulting in lower electrical consumption.
The variable frequency drive benefits extend to cost savings as well. In applications with high energy usage, the reduction in energy consumption can lead to significant financial savings. For instance, a 25-horsepower motor running 23 hours per day can save approximately $5,374 annually by using a VFD. These savings can be so substantial that they often result in a shortened payback period, making the initial investment in a VFD control panel a financially sound decision.
Equipment Protection and Safety
VFD control panels offer robust protection for your pump station’s motors and equipment. One of the key motor control VFD advantages is their ability to shield motors from damage caused by voltage sags, overloads, and other electrical disturbances. By tailoring and limiting torque, VFDs prevent motors from exceeding safe torque limits, thereby safeguarding machinery and equipment from potential damage.
This protective capability also translates to reduced maintenance costs and extended equipment lifespan. By minimizing the stress on motors and other mechanical drive components, VFDs help ensure that your equipment remains in good working condition for longer periods, reducing the frequency and cost of repairs.
Operator safety is another critical benefit of VFD control panels. By providing a controlled environment for motor operation, VFDs help create a safer workplace. Additionally, VFDs can help industries comply with safety regulations and standards, reducing the risk of accidents and injuries.
Improved Process Control and Reliability
Variable frequency drives offer precise speed control, which is essential for optimized process control and improved product quality. By allowing for fine-tuned adjustments to motor speeds, VFDs enable your pump station to respond accurately to varying demands, ensuring that processes run smoothly and efficiently.
The reliability of your pump station is also enhanced with VFD control panels. By reducing the risk of motor failure and downtime, VFDs contribute to a more dependable operation. This reliability is further supported by the flexibility VFDs offer in process control, allowing for remote adjustments of motor speeds and torque as needed.
Improved process control and reliability lead to increased productivity and efficiency. With VFDs, your pump station can operate more effectively, reducing downtime and allowing for quick recovery in case of a fault. This means that your operations can continue with minimal interruptions, maximizing output and efficiency.
By integrating these new sections, the article now provides a comprehensive overview of the numerous benefits of VFD control panels, from energy savings and cost reductions to enhanced equipment protection and improved process control.
Common Applications for VFD Control Panels
Water Pressure Boosting: Water pressure booster pumps are usually specified to run at the best efficiency point (BEP) at maximum flow. Traditionally, valves have been used to increase system pressure and attempt to optimize flow control; however, this design has often proven to cause the pump to operate inefficiently and waste energy. VFDs provide more control by allowing you to operate the motor at variable frequencies, thus providing dynamic control over the flow rate variations. VFDs can be configured to slow the pump motor down for low demand periods and speed it up during high demand periods. Not only will the pump run more efficiently, there will be an overall reduced cost on energy consumption over the lifetime of the pump. Electric motors, when paired with VFDs, achieve significant efficiency improvements in these applications.
Sewer Pumps: When pumping abrasive media like sewage, pumps that run on a fixed speed are more susceptible to damage. By controlling pump speeds, VFDs are a better choice since they can adjust to the changing demands and they can reduce the risk of blockages caused by debris and solids in the sewer system. If the flow rate is too high, it can cause turbulence and hinder efficient sewage transport, while too low a flow rate might allow solids to settle. VFDs can reduce the need for control valves, which often require regular maintenance. This can also save energy and reduce wear and tear on pumps, leading to lower operating costs.
Storm Drainage: Storm drainage systems often experience fluctuating water levels. A VFD allows for precise control of pump speed, which can help manage varying water flows effectively. This ensures that the system can handle both heavy storms and lighter rainfalls. Being able to gradually ramp up and down the motor speed allows a VFD to minimize the mechanical stress on the pump and associated equipment. Water hammer can occur when there is a sudden stop or change in water flow and this causes pressure surges, but a VFD minimizes the mechanical stress on the pump and associated equipment. This also reduces wear and tear, prolonging the lifespan of the system.
Agricultural Irrigation: Agricultural irrigation systems usually contain zones segmented by field size, crop type, and/or crop maturation date. The various zones within the system may contain a wide range of different pressure and flow rate requirements for each zone. In the past, these systems might require a combination of valves, a small jockey or PM pump, and one or more main pumps to work together. VFDs offer more flexibility by enabling the system to adjust the speed of the pump based on the specific flow rate and pressure requirements for each zone. Not only does the VFD eliminate the need for the small jockey or PM pump, it also conserves energy and water over the course of the growing season.
Types of VFDs
-
Voltage Source Inverter (VSI): VSI VFDs are most commonly used in industrial applications. They have a fairly simple design but are both reliable and cost-effective. Because they’re limited in high-performance dynamic control compared to other types of VFDs, the VSI VFD is best suited for applications requiring constant torque (for example, conveyors and pumps). If you’re looking for the most standard/basic VFD, this would be the most efficient and cost-effective option.
-
Current Source Inverter (CSI): CSI VFDs generate constant current DC and convert it into a variable AC output. They are often used in high-power applications like large compressors and heavy machinery because it is able to provide a high power output and inherent short-circuit protection. However, they are bulky and can be expensive and less efficient than VSI drives. If you are looking for a VFD best for high-power and heavy duty applications with high torque, this would be the best option.
-
Pulse Width Modulation (PWM): PWM VFDs generate variable frequency and voltage by adjusting the width of pulses in a DC signal. This kind of VFD offers precise control over motor speed, high efficiency, and smooth operation but it can generate electrical noise which may require additional filtering in sensitive environments. This VFD is preferred for precise motor control and energy efficiency across diverse applications. Additionally, the use of a frequency control potentiometer in PWM VFDs allows for precise speed control, enhancing user control and system efficiency.
Choosing the Right VFD for Your Pump
When choosing a VFD for your pump, there are a few things you might want to consider:
-
Application: Match the pump type to the system
-
Flow/Pressure Needs: Different VFDs can be more suitable for different pressure needs
-
Fluid Type: Ensure compatibility with the fluid (eg: clean water vs. wastewater)
-
Energy Efficiency: Use a VFD for fluctuating demands to save energy
-
Maintenance: Consider cost, maintenance, and long-term efficiency
-
Input Line Power Supply: Ensure the input line power supply is adequate to power the VFD panel and provide essential protection features. This includes enabling the circuit breaker to manage functionality and safety during short circuits or overloads, ensuring operational reliability and operator safety.
-
Full load amps (FLA): The FLA of the motor determines the size of the VFD. The VFD's current rating should match the motor's FLA. You can also choose a VFD with a higher current rating than the motor's FLA for safety and reliability.
-
Horsepower: VFDs have a stated HP range, so you can choose one that's appropriate for your application.
-
Voltage: In the US, low voltage applications typically use 208 VAC, 234/240 VAC, or 480 VAC for three-phase input motors.
-
Speed range: Motors shouldn't be run at less than 20% or more than 20% of their rated speed.
-
Load Type: The type of load on the motor determines the size and cost of the VFD. For example, constant torque loads require a VFD that can provide a high starting torque.
-
Motor rating: If your motor is more than 5–10 years old, it may be inverter rated, which means it can handle voltage spikes and lower speeds without overheating. The nameplate may indicate "CT/VT" for constant torque and variable torque, or "PWM" for Pulse Width Modulation drive.
Conclusion
A Variable Frequency Drive (VFD) is a versatile and energy-efficient device that regulates the speed of torque of pump motors by adjusting the motor’s input frequency and voltage. A variable frequency drive panel (VFD Panel) is crucial in maintaining the continuous operation of liquid flow control processes. VFDs have become an essential component in modern motor-driven systems because of their ability to adapt to fluctuating demand, minimize mechanical stress, and improve overall system efficiency. Other benefits that VFD panels offer include: optimizing performance, reducing energy consumption, and extending the lifespan of motors in various applications. Understanding the different types of VFDs and their specific uses can help in selecting the right drive to achieve both operational and energy-saving goals for your pump station.
Resources
-
"What is the right pump VFD?" Tyler Simmons, VFDs.com, April 13, 2023
-
"Can Any Motor Be Used with a VFD?" eMotors Direct, May 14, 2024
-
"Submersibles and VFDs: Working Together," Adam Stolberg and Chris Caldwell, Pete Duty & Associates, Modern Pumping Today, March 2020